当前位置: |
引领中国冶金迈向智能化、绿色化、低碳化、高效化------ 中冶华天一批炼铁核心技术达国内国际先进水平
    发布日期:2022-07-20
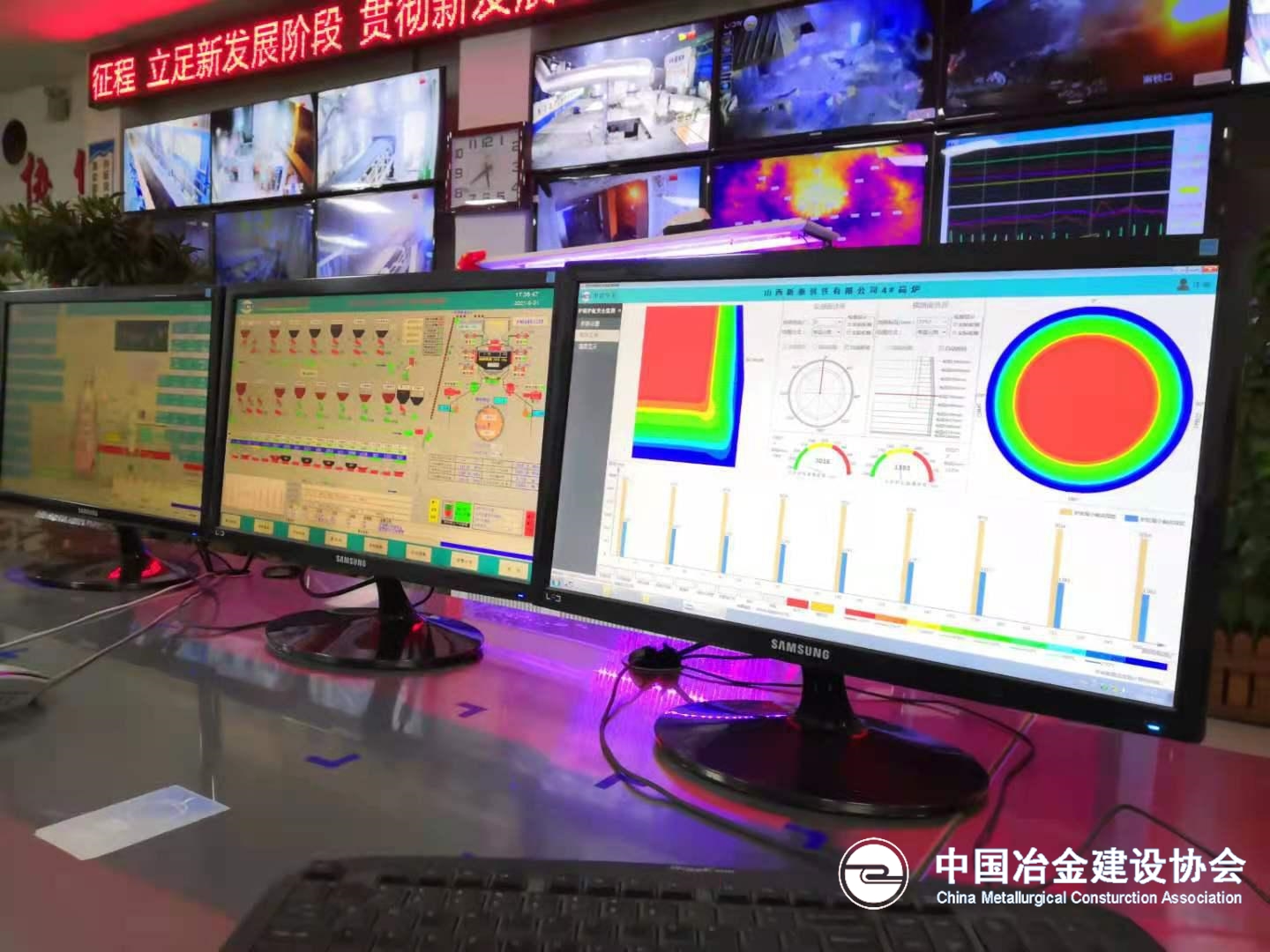
在高炉长寿、高炉智能化、高效热风炉、节能环保等方面拥有独特设计技术;掌握了当今高炉炼铁所有先进技术,尤其在1000立方米-2500立方米级高炉中有较高的市场占有率和口碑……“我们始终站在国际水平高端和冶金行业发展前沿,凭借持续的自主研发创新能力、国际一流核心技术、冶金全产业链整合集成优势,引领中国冶金实现智能化、绿色化、低碳化、高效化发展,推动实现‘钢铁强国’目标。”7月7日,中冶华天钢铁院炼铁事业部部长赵奇强自豪地说。
攻克“顽疾”保障安全稳产
2021年11月,当“抗涨防漏型高炉炉缸炉底综合安全长寿技术”被中国冶金科工集团鉴定为“国内领先”水平时,炼铁事业部全体员工的艰苦付出终获认可。
高炉炉底的密封性能直接影响高炉寿命,一旦发生问题不仅难以处理,还会造成重大安全隐患和经济损失。为攻克“顽疾”,中冶华天基于几十年高炉整体设计和工程实践经验积累,率先提出了基于炉底双层封板结构,实现高炉炉底炉缸抗涨防漏的新思路。经过不断研究、试验,“抗涨防漏型高炉炉缸炉底综合安全长寿技术”脱颖而出获得发明专利授权。该技术缓解了高炉上涨引起的炉底炉缸结构破坏和由此导致的炉底泄漏煤气问题,一定程度上提高了高炉对焦炭、煤和各种矿石的适应程度,促进了高炉长寿、安全生产和环保。
目前,该技术已应用于河北安丰、福建三钢、罗源闽光、永锋临港、河北华信、冀南文丰等十余座高炉。其中河北安丰钢铁2号高炉自投产至今,生产炉底炉缸温度检测正常,炉底炉缸状态正常,炉底板无任何上翘现象,应用效果一如预期,实现了高炉稳产长寿。
新技术实现放散煤气和除尘灰零排放
高炉生产过程中放散的煤气,为含有大量一氧化碳和灰尘的有毒、可燃物混合气体,其放散时产生的噪音和粉尘不但对大气环境直接造成污染,也浪费了煤气能源。对于高炉炉顶料罐放散煤气回收利用成为行业内迫切解决的问题。
唯因其难,方显真功。为攻克难关,中冶华天围绕料罐与煤气管网间压差大、不稳定及对管网冲击大等技术难点,创新设计了新的均压煤气回收系统和净化处理系统。通过应用检验,“高炉炉顶均压煤气净化回收利用技术”可实现放散煤气和除尘灰的零排放,放散煤气回收利用率可达到80%-100%,高效解决了高炉炉顶均排压煤气及煤气灰直接对空排放引起的大气污染问题。
该技术现已授权发明专利1项、实用新型专利5项,应用于淄博钢铁、鞍山宝得钢铁、宝武马钢、河北华信、冀南文丰、福建三钢、罗源闽光等多个大型工程。与传统炉顶均压煤气直接放散工艺相比,年可回收煤气千万立方米、创经济效益达数百万元。
自主研发助力绿色发展
传统的高炉煤粉喷吹工艺系统,存在瞬时输送量波动大、生产成本高等缺点。中冶华天自主研发出了新型下出料浓相均匀自动高炉煤粉喷吹技术,通过独特的工艺流程设计,实现高炉煤粉喷吹系统一键式自动均匀喷吹、浓相远距离输送,解决了自动化程度不高、输送量波动大、输送成本高等问题。
如今,这项被中冶集团鉴定为“国际先进”水平的技术,已成功应用于防城港钢铁、柳钢、长钢、河北华信、冀南钢铁等工程设计项目。宝武马钢二铁总厂4座高炉年喷吹煤粉约130万吨,可替代约104万吨焦炭,节约炼铁生产成本4亿多元;采用浓相输送可节省5000万标方氮气消耗,可节省煤粉喷吹成本约100万元;采用自动喷吹后减员四分之三,年节约人工成本120万元,且工作强度降低,减少了环境二次污染及烟气排放,经济效益、环境效益显著。
据了解,面对当前钢铁行业智能化发展趋势,中冶华天正围绕炼铁高炉系统大力开发可视化、数字化和智能化相关技术,其中已突破部分技术并在生产一线落地应用,如“高炉炉底炉缸侵蚀智能监测系统”已在钢铁企业实施应用;大力推进钢铁低碳技术的研发与应用,其中高炉喷吹焦炉煤气的工艺设计、关键技术研发相关示范工程正努力推进中。(来源:中冶华天 黄苹)